How To Build a 5-second 426 cubic inch Keith Black Racing Nostalgia Funny Car Hemi
July 2020 • By Nick Davies, ICEAutomotive.co.uk
photos Nick Davies, Scott Barnes & MattWoodsPhotography.com
Nostalgia drag racing has seen steady growth over the last decade or so and that growth didn’t escape the notice of UK racer Tim Garlick who, wanting to go quicker and faster than his ‘fastest Rover-powered race car on the planet’ (at the time), looked at the momentum of the US-based Nostalgia Funny Car scene and made a phone call….
Tim called Rob Loaring and myself at ICEAutomotive.co.uk after which the three of us looked into the possibility of trying to get a Nostalgia Funny Car Class off the ground in the UK. The best way appeared to be to put money where mouth was and build one from scratch—money talks remember. The plan we hatched was to build ‘Apache’ a 1977 Pontiac Firebird-bodied Nostalgia Funny Car in the spirit of how the cars were back in the day while complying with the tried and tested formula that was being successfully applied in the US.
The build of the car itself is the subject of a different article, but this article focusses on the heart of the Funny Car and, true to the formula of the period, would be based on a cast-aluminium Keith Black block and cast-aluminium cylinder heads. The target? A flagship for the new class and Europe’s first 5-second Nostalgia Funny Car. Maybe not an earth-rotating goal but it had never been done in Europe and it was an achievable target to aim at. Achievable goals keep teams motivated.
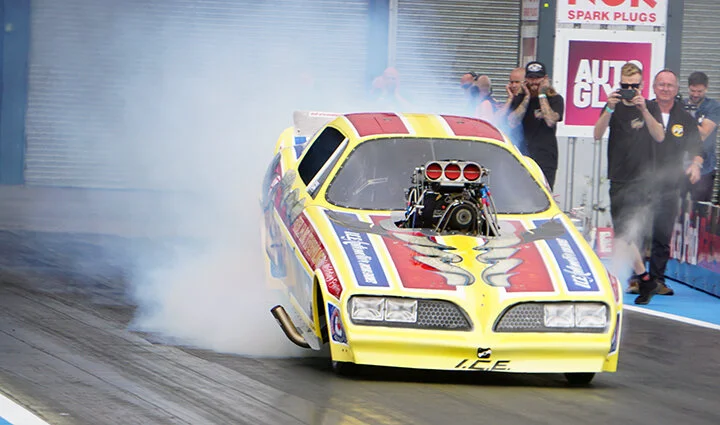
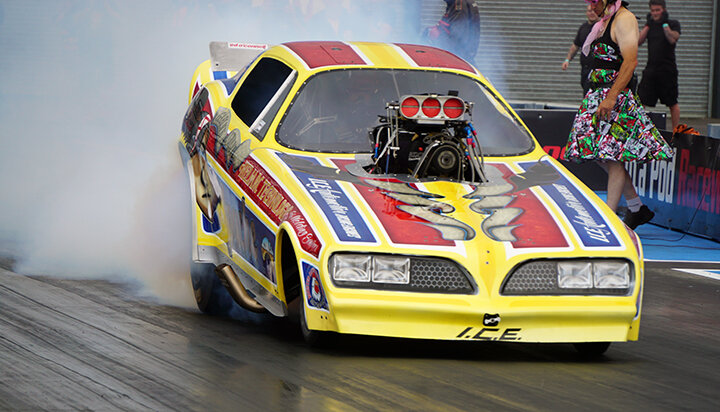
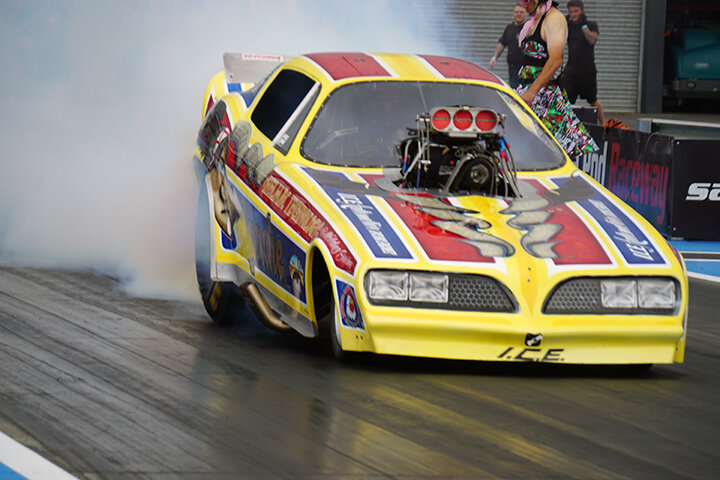
There have been huge advances in technology since the halcyon days of the 70s and 80s Funny Cars, considered by many to be the golden age of nitro racing, but the Apache team wanted to keep the aesthetics and key components of the new build as a respectful tribute to the past. While incorporating the period-correct cast engine components, no compromises were made on the internals and the I.C.E. philosophy of build it right, build it once was faithfully followed. Appreciating the need for ‘between-run maintenance’, the desire for ‘checking and confirming’ rather than ‘removing and replacing’ meant the team made a huge effort to build as good, robust and durable an engine as possible before a single part was ordered or fabricated. Research and understanding have always been considered of more value than what is alleged to be the current hot-ticket or fashion. Rob and myself went to work.
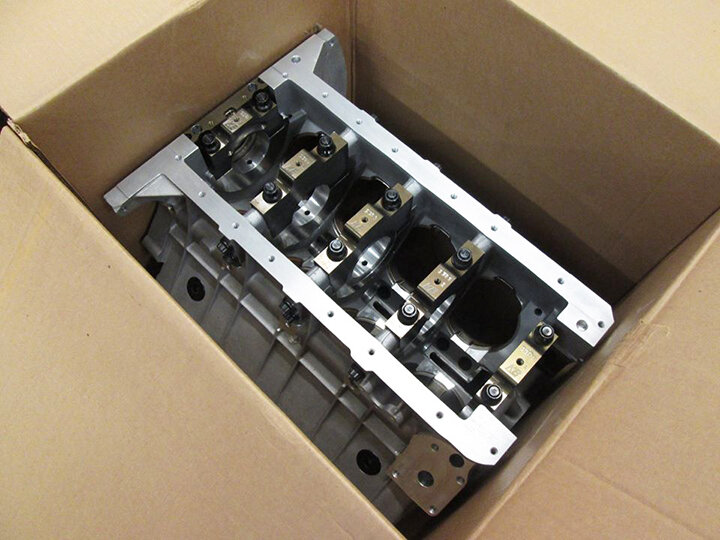
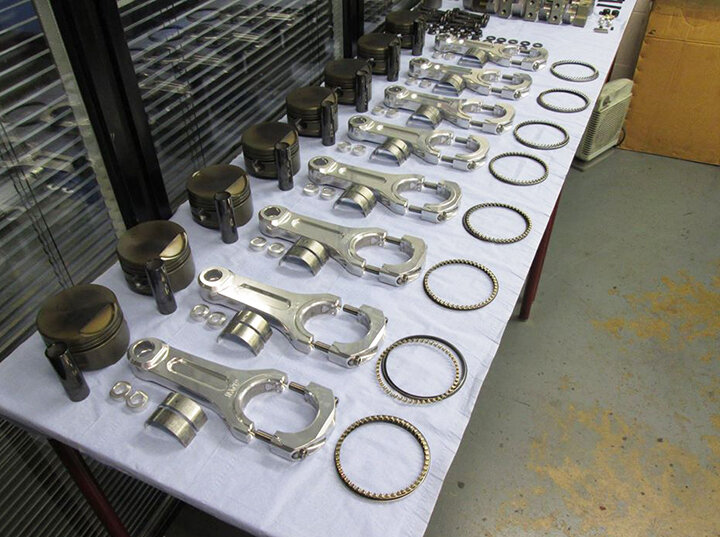
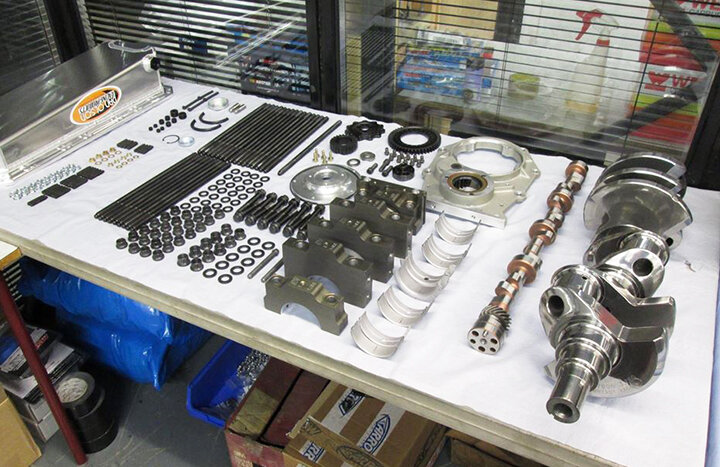
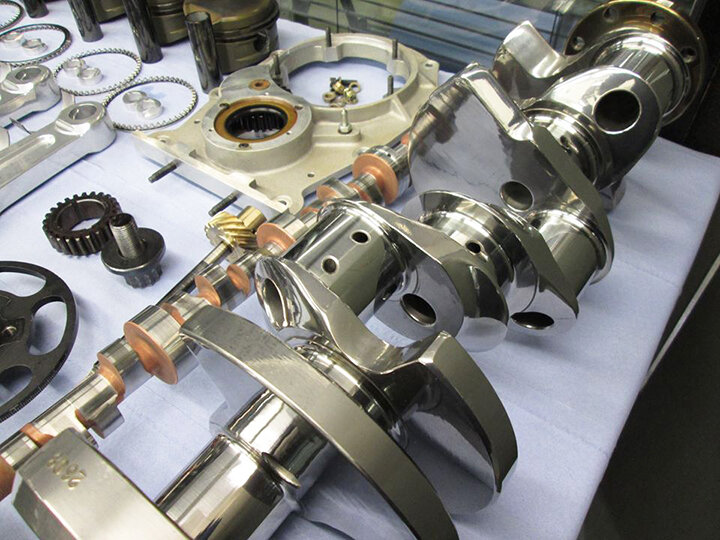
A new water block was sourced from legendary manufacturer Keith-Black.com, heads and rocker system from StageV.com, and then we relied on tried and trusted suppliers BryantRacing.com for the crank, MGPConnectingRods.com for rods, JEPistons.com for pistons, BlowerDriveService.com for the blower, Dan OlsonMotorSports.com for the oil pan and ARP-Bolts.com for all important fasteners.
Once all the key components were received, the work moved from the calculator to the flow bench and machines. No straight assembly here. In our view, engines should be application specific and it is impossible for manufacturers to accommodate all applications and unfair to ask them to, so, like many engine builders, we consider major components, such as blocks, heads and induction systems often as semi-finished.
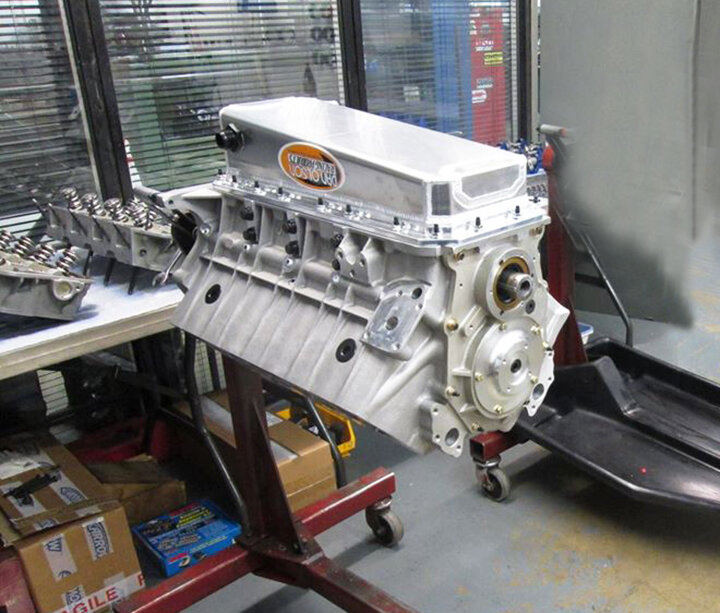
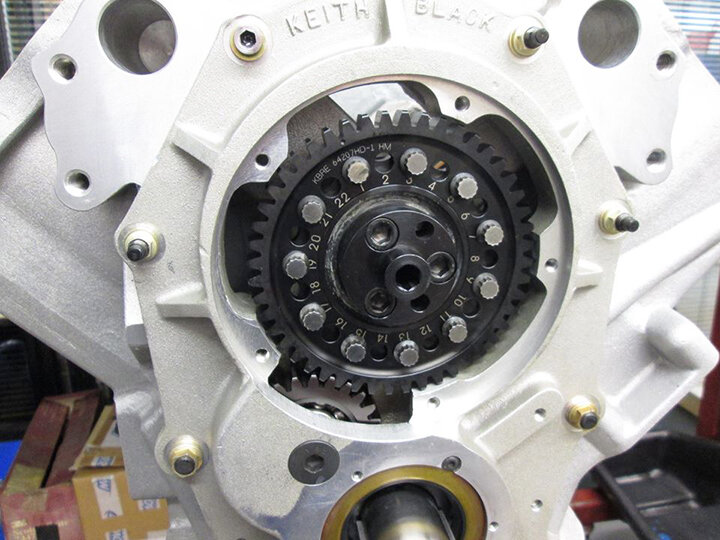
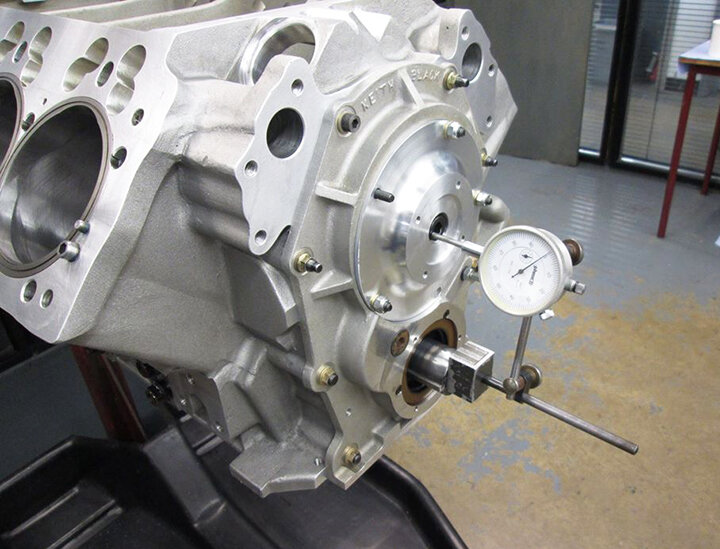
The engine block needed little work beyond some internal oiling modifications and a finish hone and the last dummy build indicated that we were in good shape. The heads were a different story. Stage V makes a great product. If they had a ‘tick-box’ menu for fuel-type, engine size, clutch-style, RPM range etc, they would make a hundred different configurations of the same casting.
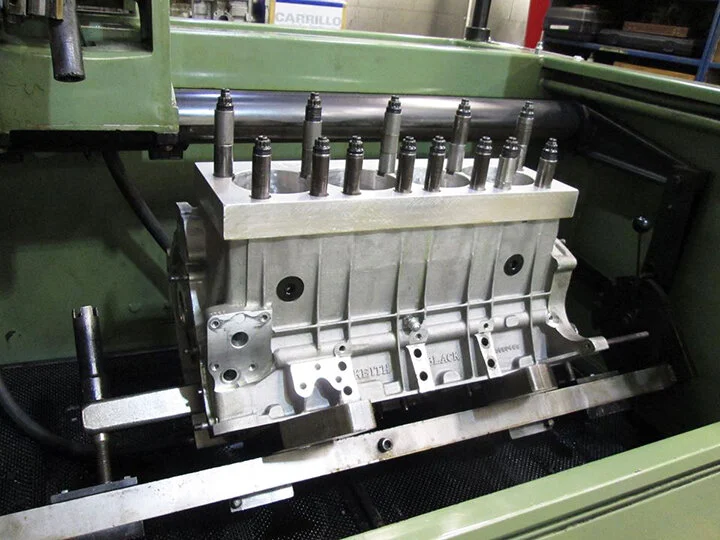
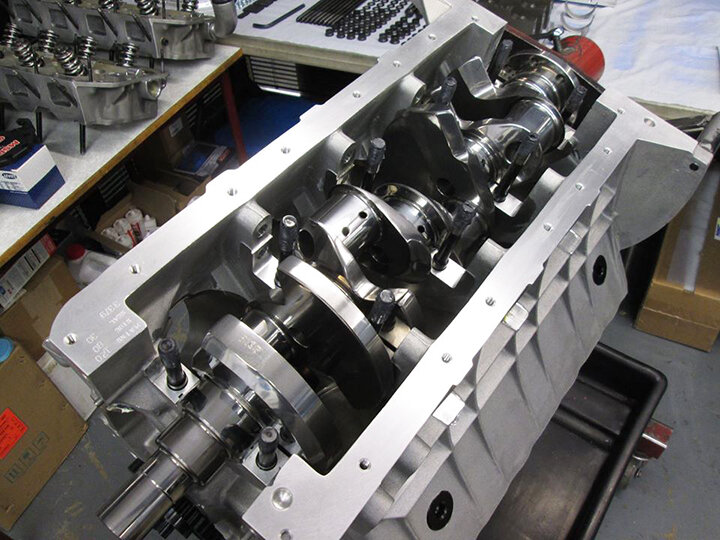
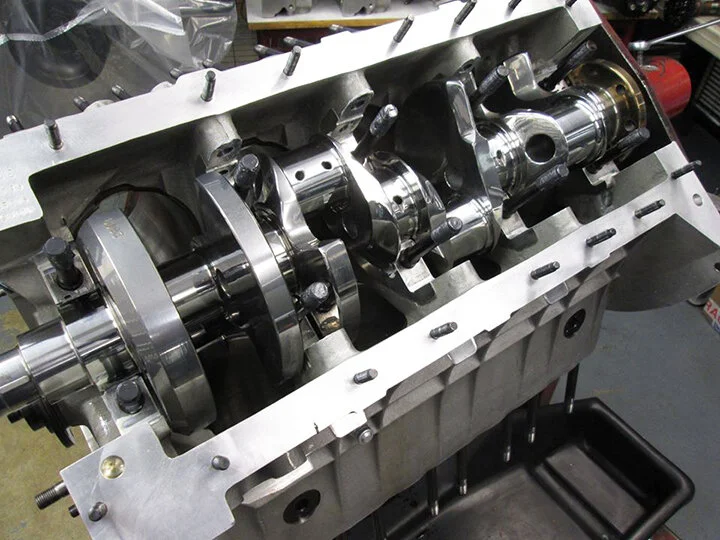
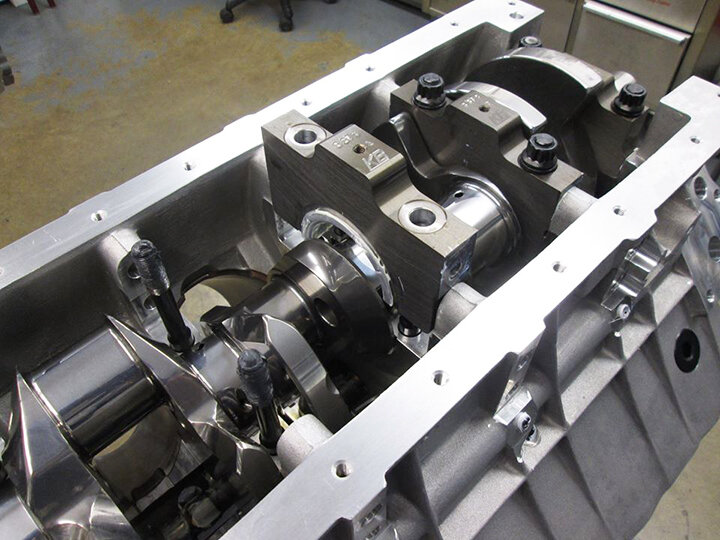
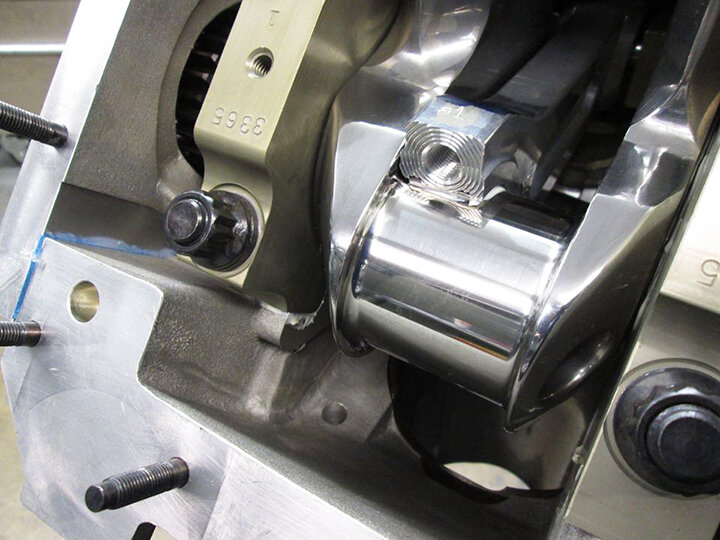
We were building a relatively small 426 ci to run on up to 90-percent nitro with a glide-clutch needing a hugely responsive throttle off idle. One of our port cross-section molds indicated that the ports were way too big for us so we machined and fitted spacers to suit both the heads and intake manifold, reducing the cross-section appreciably. Many hours on the flow bench, a few hours on the milling machine, some hand finishing and a couple of port molds later and we were in better shape, as were the ports.


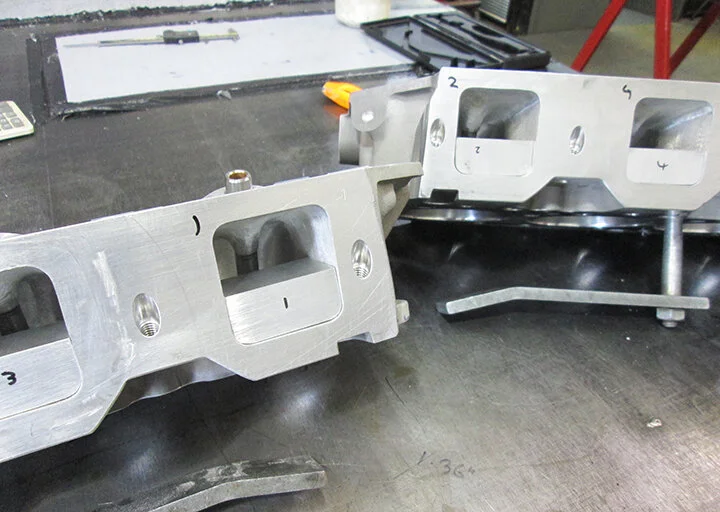
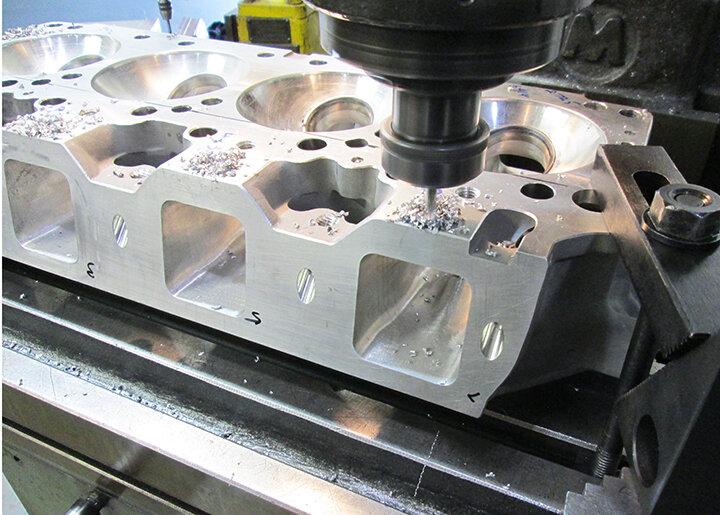
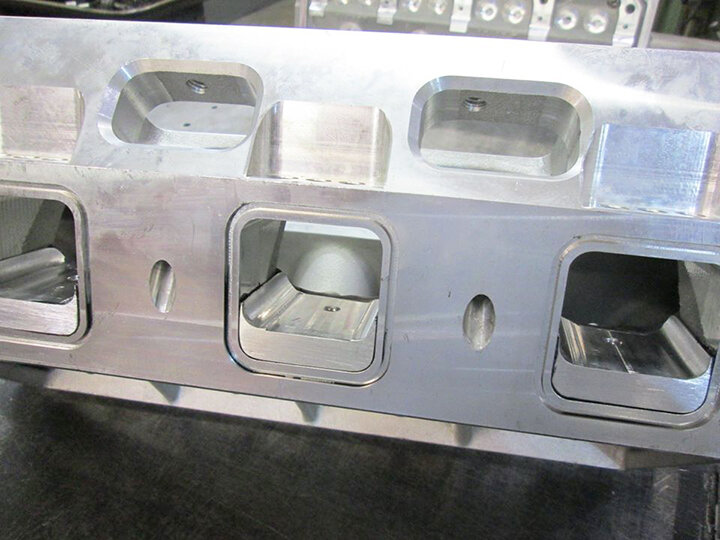

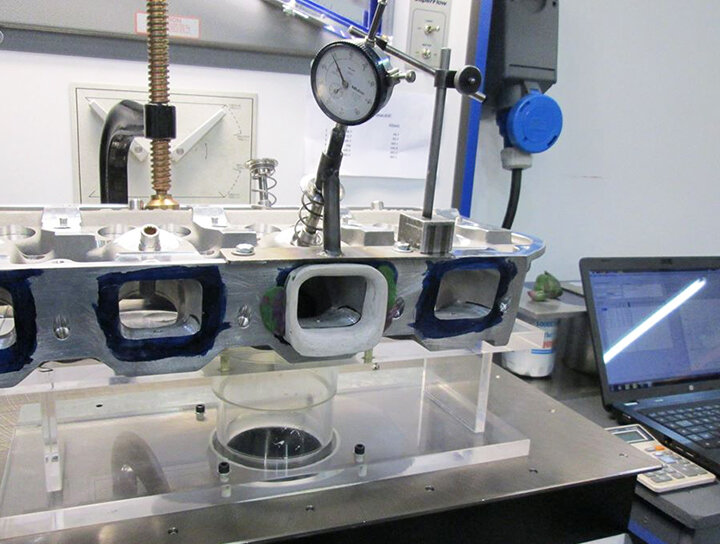
Here, we can see the port, as supplied by StageV.com and the inserts we fabricated and fitted for the intake runner in the cylinder head and the corresponding port of the intake manifold, based on port molds and calculations as to the final targeted runner cross section to achieve our desired intake volumes. Actual flow bench data suggested that we were in the right ballpark with our calculations.
It wasn’t until a little later that we tried to get extra clever with the induction side. We found during the first test sessions that the rear cylinders weren’t working as hard as the fronts. This was evident from the jetting pattern we were having to run in order to get similar looking plugs and logger exhaust gas temperatures from the trusty Racepak.

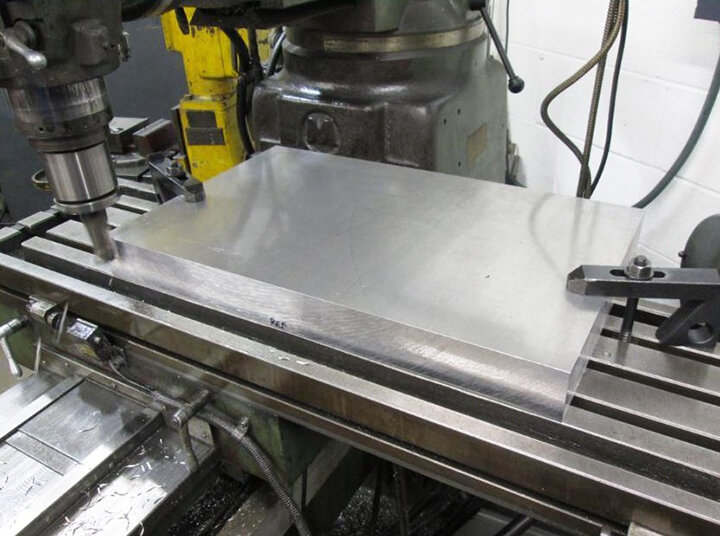
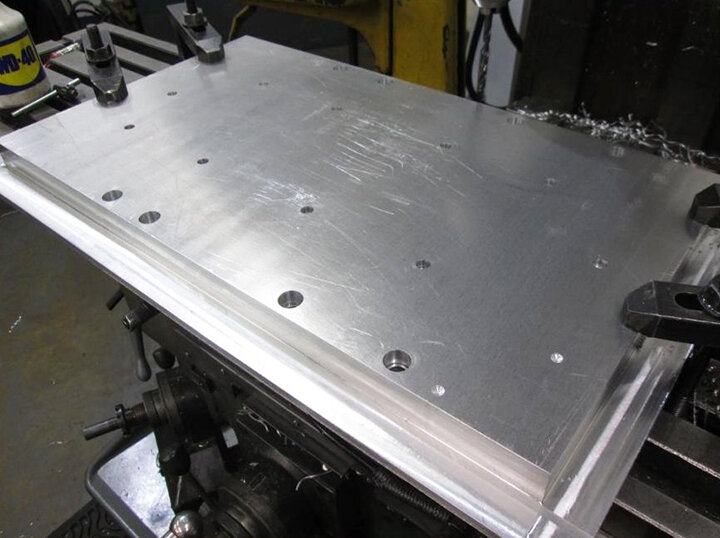
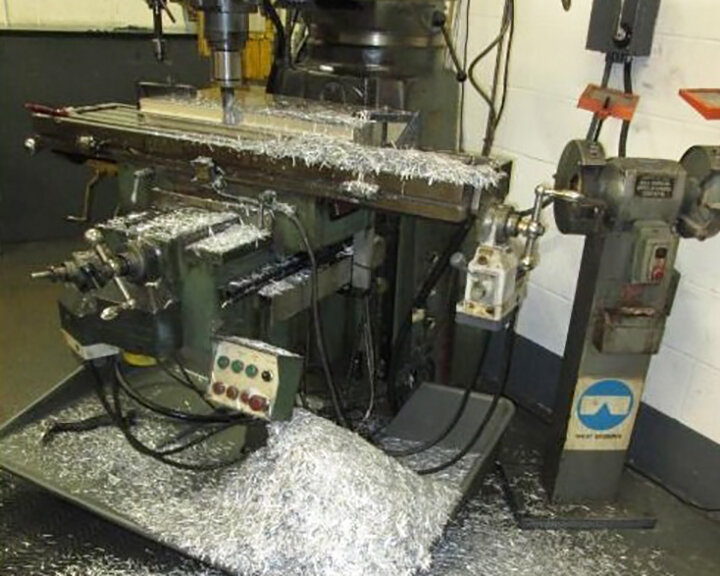
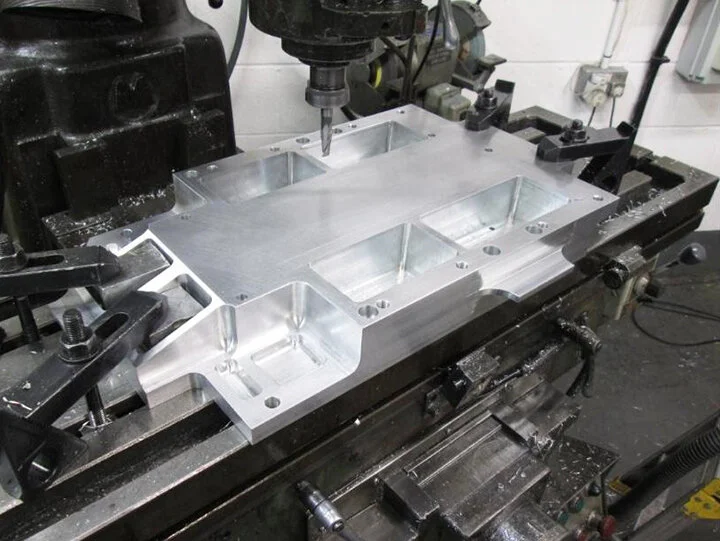
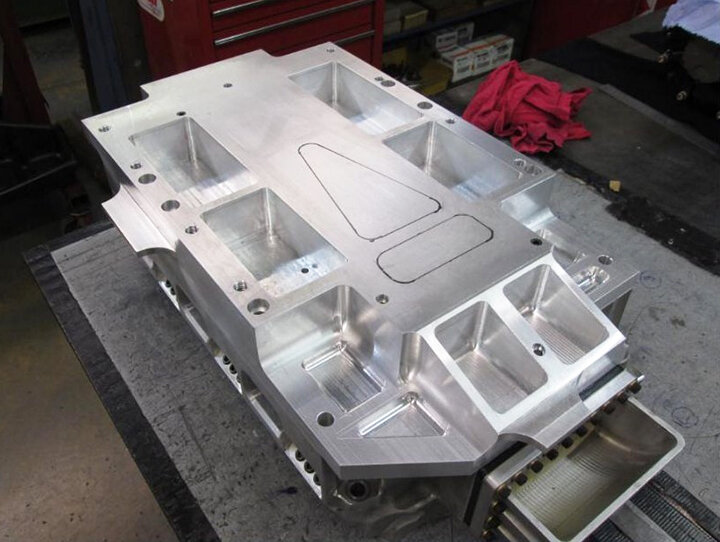
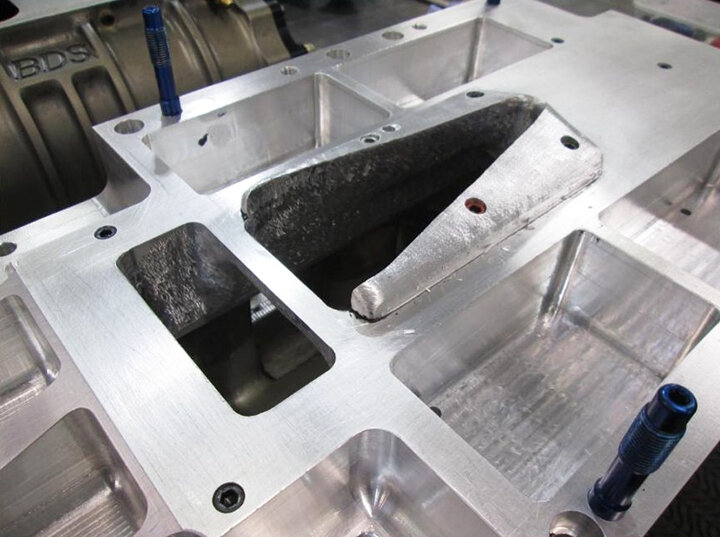

The 83 lb chunk of aluminum was taken and manually machined to exploit the allowable height restrictions enabling us to straighten the intake flowpath and better distribute the air/fuel mixture between cylinders. The discharge shape on the underside of the blower was mirrored in the spacer.
Our answer? Straighten the flow path by using the maximum height available in the rules and fabricating a spacer to sit between the blower and intake manifold. Starting with an 83 lb piece of billet aluminum, 55 lb of chips later we had a proprietary spacer. It worked well….
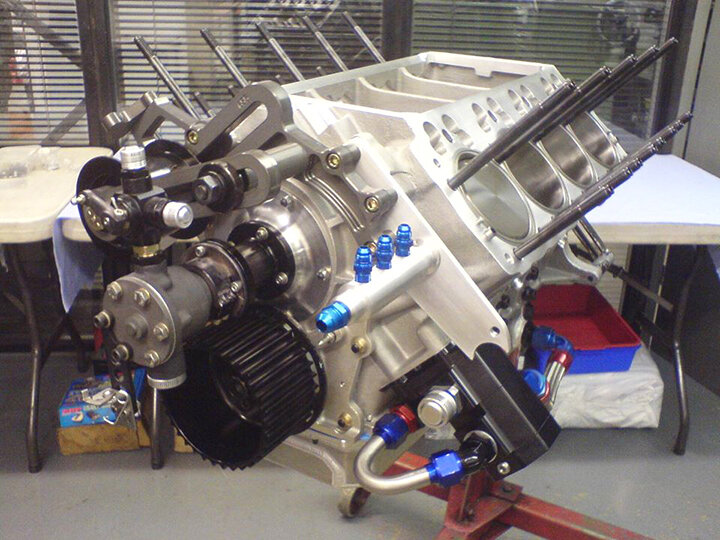
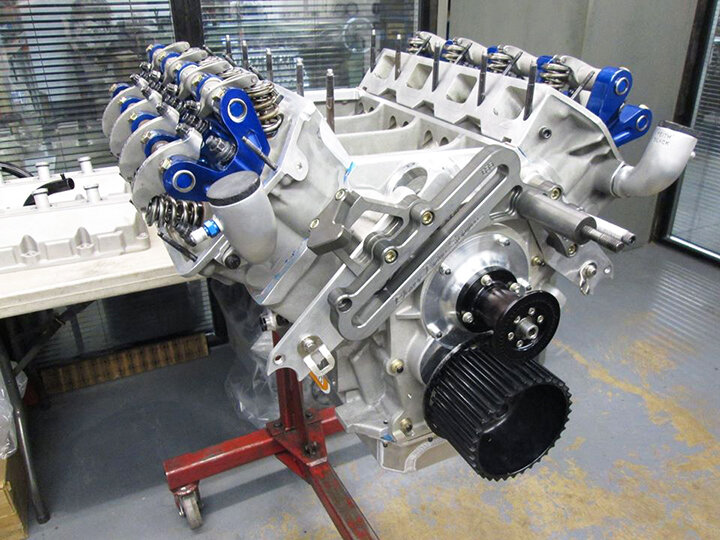
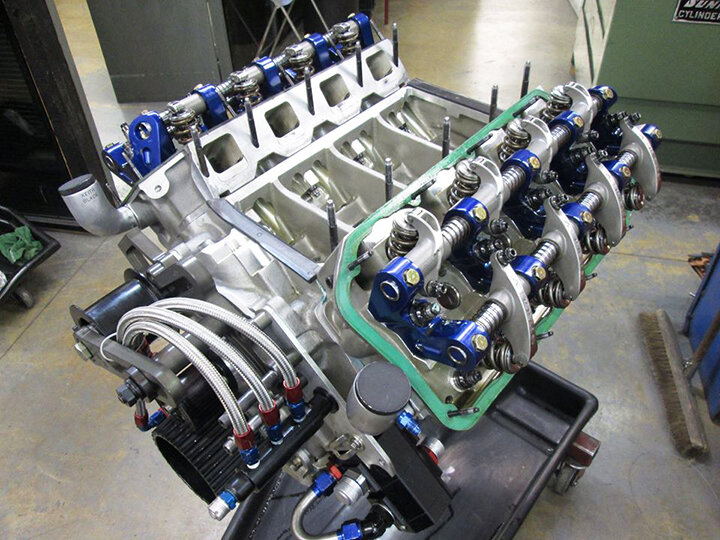

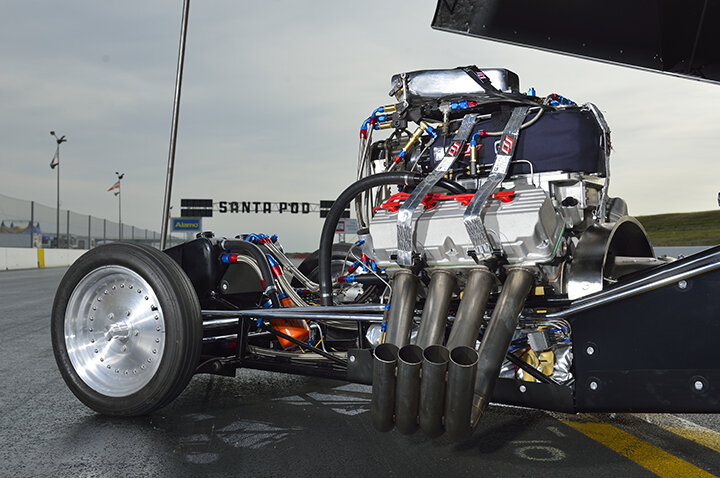
Granted, it’s not the cheapest way to go racing, but there is something about an all-new cast KB hemi that reminds us of what we dreamed of as kids,
So far, Tim Garlick’s ’77 Pontiac Nostalgia Funny Car has run a best of ET of 5.96 and a fastest speed of 237 mph. Photo Matt Woods.
Eventually, mission accomplished. Europe’s first and so far only 5-second Nostalgia Funny Car with a best of 5.96 seconds and 237 mph (different passes). Not world beating, we accept. But as a pretty faithful re-creation without the ‘drop-sides’, aero assistance, billet block, heads and clutch and at a total damage cost-to-date of two pistons—that’s an aggregate, not per year—and with potential for a whole lot more performance, Tim, the customer, considers it job well done. Ultimately, that’s what matters…